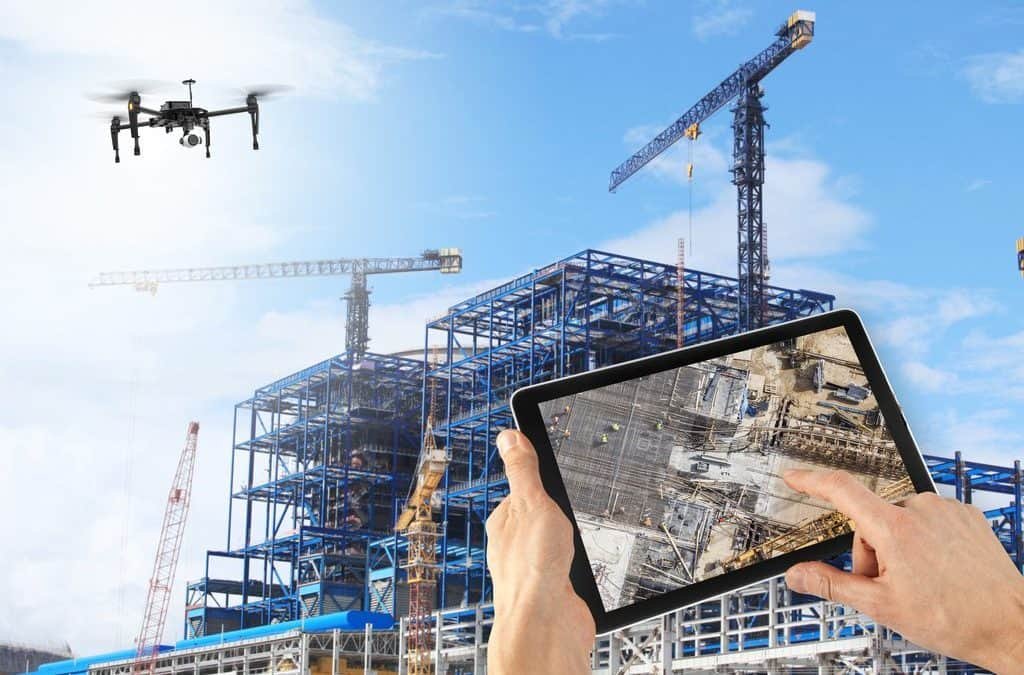
How Drone Technology Is Influencing High-Rise Construction Costs
In the heart of a bustling city skyline, steel skeletons of future skyscrapers rise into the clouds. Cranes swing like mechanical arms, lifting tons of materials to dizzying heights. Below, engineers, architects, and workers bustle with purpose. Amid all this orchestrated chaos, a quiet revolution is unfolding, one that buzzes just overhead.
That revolution is drone technology.
What began as a military innovation and hobbyist gadget has rapidly transformed into one of the most powerful tools reshaping the construction landscape. Drones, technically known as unmanned aerial vehicles (UAVs), are no longer novelties. They are data-collecting, efficiency-boosting, cost-saving devices now central to the high-rise construction industry. Their influence is as quiet as their propellers, yet their impact on project timelines, labor costs, and safety protocols is thunderous.
So how exactly are drones being used in high-rise construction, and what ripple effects are they creating in terms of costs, efficiency, and safety? Let’s take a deeper dive.
When Did Drones Enter Construction?
Drones began edging into the construction sector in the early 2010s. Initially met with curiosity and skepticism, they found their first significant use cases in site surveying and aerial photography. By 2015, a few pioneering firms started using drones regularly to track construction progress and generate topographical maps.
The turning point came when drone technology advanced in tandem with improvements in high-definition cameras, GPS precision, LiDAR sensors, and real-time data transmission. Suddenly, drones were no longer just tools for pretty aerial shots, they became data engines capable of scanning sites, assessing structural integrity, and even predicting delays before they occurred.
Fast-forward to today, and drones are mainstream in construction workflows. As of 2024, over 75% of large construction firms in North America report using drones for at least one phase of their projects.
How Are Drones Used in the Construction Industry
Drones have evolved into multifaceted tools that play vital roles throughout a high-rise building’s lifecycle, from initial planning to final inspections.
1. Surveying and Mapping
One of the most valuable drone applications in high-rise construction is aerial surveying. Traditional land surveys, especially for large or complex urban sites, can take weeks. Drones can reduce this to a matter of days or even hours.
Using photogrammetry or LiDAR sensors, drones can generate precise 3D topographical maps. These maps provide engineers with accurate terrain data, helping them design foundations and drainage systems with greater accuracy.
2. Monitoring and Progress Tracking
Supervising a skyscraper from the ground is like trying to see the forest through the trees. Drones offer a bird’s-eye view of the entire site, capturing time-lapse progress updates. These visuals help project managers stay on schedule and communicate progress with stakeholders, without climbing to the 40th floor.
Some drone systems even integrate with Building Information Modeling (BIM) platforms to automatically compare “as-built” conditions to the original design, identifying discrepancies in real-time.
3. Safety Inspections and Hazard Detection
High-rise sites are inherently dangerous. Drones equipped with thermal imaging can detect structural weaknesses, overheating electrical systems, or gas leaks, without exposing human inspectors to harm.
Routine safety checks with drones minimize the need for scaffolding or rope-access inspections, reducing risk and improving compliance with OSHA regulations.
4. Logistics and Material Tracking
By flying over construction sites and feeding real-time video, drones help supervisors track equipment and materials. In complex sites with multiple storage areas and delivery trucks, this live overview can prevent delays caused by misplaced items or inefficient workflows.
5. Marketing and Client Engagement
From a marketing perspective, drones provide stunning visuals for promotional videos, investor updates, and client tours. A 360-degree panoramic view of a high-rise under construction is far more persuasive than a spreadsheet.
Impact on High-Rise Construction Costs
Drones do more than add value, they subtract cost. Here’s how drone technology is directly influencing high-rise construction expenses.
1. Labor Savings
Surveyors, inspectors, and site supervisors traditionally require significant time and manpower to complete tasks drones can perform in a fraction of the time. A single drone operator can do the work of multiple surveyors and inspectors, significantly cutting down labor costs, particularly for large, high-rise projects.
According to industry reports, drone usage can reduce surveying and inspection labor costs by up to 60%.
2. Minimized Delays
By offering real-time insights and progress tracking, drones help prevent expensive delays. A project delayed by even a week can cost millions in additional labor and rental fees. Drones help maintain timelines by quickly identifying potential issues before they escalate.
3. Reduced Rework
BIM-integrated drones help verify that construction matches design specifications. This early detection prevents costly rework down the line. For high-rise buildings, where structural misalignments can become catastrophic at scale, the value of this accuracy is immense.
4. Enhanced Site Planning and Utilization
Aerial overviews help optimize crane placement, worker flow, and material staging areas, all of which contribute to smoother logistics. Time saved in logistics equals money saved in execution.
5. Improved Safety = Lower Insurance Premiums
Reduced incidents mean fewer claims and potentially lower insurance premiums. Drones help identify unsafe areas early, reducing the likelihood of injuries and associated costs.
The Pros and Cons of Drones in Construction
Like any technology, drones bring both upsides and challenges.
✅ Pros:
-
Time Efficiency: Complete site surveys in hours instead of days.
-
Cost Reduction: Lower labor, reduced rework, and optimized logistics.
-
Safety Improvement: Limit human exposure to high-risk areas.
-
Data Accuracy: High-resolution imaging and 3D modeling for precision planning.
-
Transparency: Easy stakeholder reporting and visual updates.
❌ Cons:
-
Initial Costs: High-quality drones with advanced sensors can be expensive.
-
Training Requirements: Operators need FAA certification and specialized training.
-
Privacy and Legal Concerns: Urban construction sites may raise privacy issues.
-
Weather Dependence: Rain, strong winds, or fog can ground drones.
-
Data Overload: Large volumes of imagery and sensor data require robust storage and analysis systems.
How Big Is the Construction Drone Market?
The construction drone market is booming, and it’s only going up, much like the buildings it helps construct.
In 2022, the global construction drone market was valued at around $4.8 billion, and it’s projected to reach over $14 billion by 2030, growing at a compound annual growth rate (CAGR) of approximately 15-17%.
North America and Europe currently lead in adoption, but Asia-Pacific is catching up rapidly, driven by massive urban development in countries like China, India, and Southeast Asia.
Major players in the drone construction market include DJI, Parrot, Kespry, Trimble, and PrecisionHawk, alongside a growing number of construction-specific drone software startups such as DroneDeploy, Propeller Aero, and Skycatch.
The Human Element: A Real-World Case Study
Let’s bring all this theory to life with a real example.
The Hudson Yards Project in New York City, one of the largest private real estate developments in U.S. history, integrated drone technology throughout its high-rise construction. With more than 28 acres of complex structures, the project used drones for topography, progress tracking, and facade inspections.
As a result, the developers reported:
-
A 20% reduction in site survey costs
-
A 30% increase in overall project efficiency
-
Enhanced worker safety with fewer scaffold-based inspections
Without drones, tracking such a dynamic site would have required hundreds of personnel working around the clock. Instead, much of it was handled by a few drone teams.
Future Horizons: What’s Next for Drones in High-Rise Construction?
As technology evolves, the future for drones in construction is even more promising. Here are a few trends to watch:
1. AI-Powered Analytics
Next-gen drones will integrate AI to automatically detect defects, predict material needs, and suggest design adjustments on the fly.
2. Autonomous Swarms
Multiple drones working together autonomously, each assigned to specific sections of the site, will become more common, enabling round-the-clock data collection.
3. Drone-Based Deliveries
In remote or vertical construction, drones could eventually deliver light materials or tools directly to upper floors, eliminating hoist delays.
4. Integration with Digital Twins
Drones will feed live data into digital twins, real-time virtual models of buildings, which will update automatically as construction progresses.
A Sky-High Return on Investment
High-rise construction is inherently complex and costly, but drone technology offers a smarter, safer, and more efficient way to manage it. From reducing labor costs to enhancing safety and ensuring precision, drones are proving that even the sky isn’t the limit.
As adoption becomes more widespread and capabilities continue to grow, drones won’t just be part of the construction process, they’ll be central to it. For builders of tomorrow’s skylines, success may soon be measured not just in floors built, but in data captured from 400 feet in the air. image/north-construction